The resistance of plastic slide binders to wear and tear can vary based on their quality, design, and the specific materials used in their construction. Here are some factors to consider:
Material Quality: Explore the molecular architecture of the plastic polymer, scrutinizing polymer chain length, crystallinity, and copolymer composition. Inquire about the specific impact modifiers used to enhance toughness and the presence of any proprietary additives that contribute to chemical stability and resistance against environmental factors. Request comprehensive data on the polymer's modulus of elasticity and elongation at break to understand its mechanical properties in detail.
Thickness and Gauge: Investigate the manufacturing process intricacies, including extrusion parameters and post-extrusion treatments, to grasp the nuanced variations in thickness. Delve into the correlation between gauge and load-bearing capacity, considering the implications of polymer orientation during extrusion. Explore stress analysis models applied during design to ensure uniform thickness distribution, accounting for any variations in molecular density across the binder's cross-section.
Flexibility: Conduct a molecular dynamics simulation to understand the polymer's behavior under repeated bending, taking into account factors such as entanglement density and cross-linking efficiency. Examine the binder's response to dynamic mechanical analysis, mapping out the storage and loss moduli to identify the transition between the glassy and rubbery states. Investigate the impact of temperature on the polymer's viscoelastic properties to predict its flexibility in diverse environmental conditions.
Closure Mechanism: Request detailed engineering schematics of the closure mechanism, elucidating the tolerances, clearances, and friction coefficients at play. Analyze the wear patterns through finite element analysis, simulating thousands of closure cycles to predict failure modes and optimize component geometries. Inquire about the tribological properties of the materials used in the closure system, including coefficients of friction and wear rates under different loading conditions.
Page Capacity: Employ finite element modeling to simulate stress distribution within the binder, considering varying page capacities. Investigate the impact of binder design on stress concentrations and strain limits, exploring methods to optimize load-bearing capabilities. Utilize failure mode analysis to predict potential points of weakness and assess the binder's response to cyclic loading, ensuring it can withstand repeated stresses without compromising structural integrity.
Smooth Edges: Examine the microstructure of the binder's edges using electron microscopy to assess surface finish quality. Evaluate the effectiveness of different edge-finishing techniques, such as vibratory tumbling or laser cutting, in achieving smooth contours. Analyze the coefficient of friction at the edges to determine how effectively it minimizes abrasion against documents during handling.
Resistance to Environmental Factors: Subject the binder to accelerated aging tests, replicating years of UV exposure and environmental stress in controlled conditions. Investigate changes in material properties, color, and texture, utilizing spectroscopic techniques and surface analyses. Explore the plastic's response to extreme temperature variations through thermal cycling tests, considering potential molecular rearrangements and their impact on long-term durability.
Triangle/ Round Back PVC Plastic Slide Binder for Office & School Supply-Plastic Binding Strip/Slide Binder
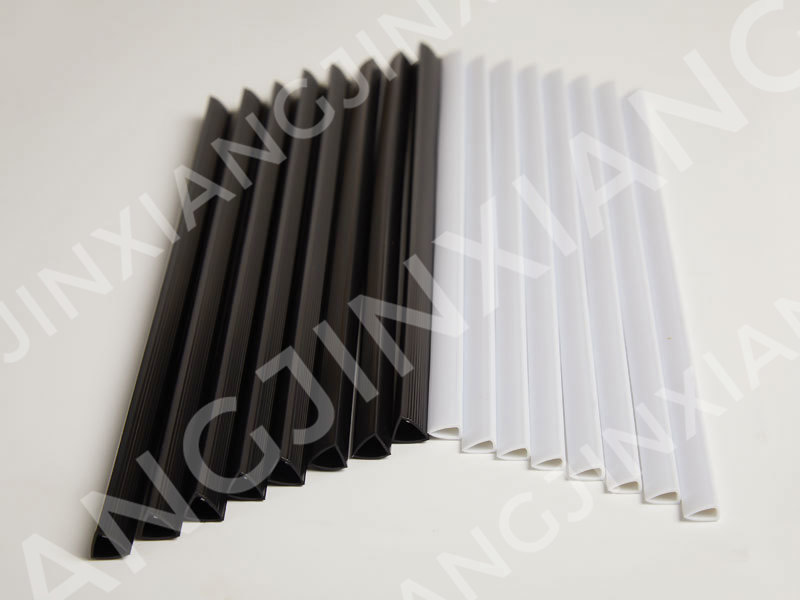
Triangle/ Round Back PVC Plastic Slide Binder for Office & School Supply-Plastic Binding Strip/Slide Binder
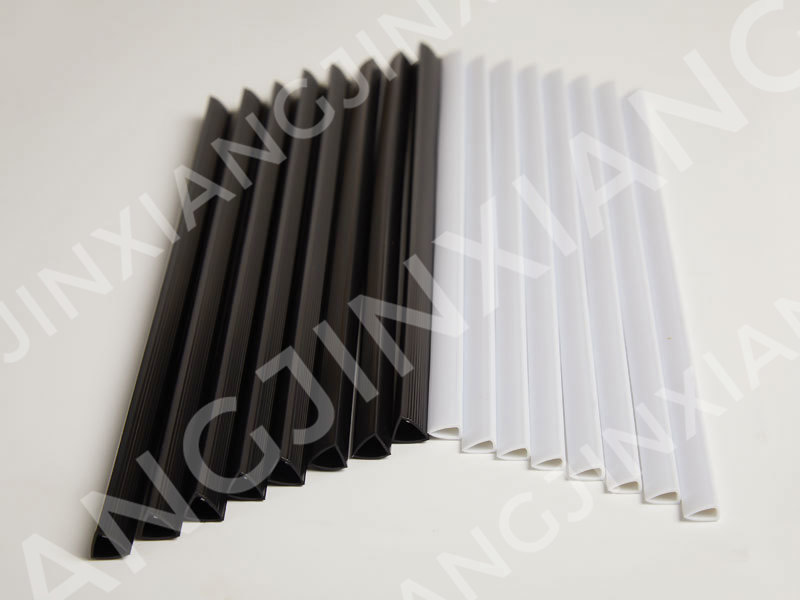